技術解説
【熱伝導シート(Zebro)とは】
熱伝導シートは、材料が持つ能力を熱伝導率(W/(m・K))で表します。また、熱伝導シートと相手面との密着度合いや材料内部の熱の伝わりにくさを熱抵抗(℃・㎠/W)で表します。
Zebroは、優れた熱伝導率ですが、使用している原料によって効率が異なります。そこで、材料の選定やサイズの合わせ込みを行い、お客様のご使用環境に合わせた低い熱抵抗へ調整させていただき、最も優れたパフォーマンスをご提供いたします。
電子部品の放熱では、熱伝導材料としてグリスやシリコーンエラストマーなどが多く用いられています。さらに、柔らかな熱伝導材料の中へ金属粉末やセラミックス粉末などのフィラー材を混入した改良品も多く使われています。
世の中の熱伝導率が高い物質として、ダイヤモンド(2200~4100※)や黒鉛(1500~5000※)が挙げられます。金属ですと、銀(約420※)や銅(約390※),金(約300※),アルミニウム(約240※)等が挙げられます。
Zebroは、材料コストや製造工程を考慮して、熱伝導材料に黒鉛を用いました。
※:熱伝導率の単位:W/(m・K)、数値は、各社製品や天然品/合成品などで大きく異なります。
Zebroの主原料である黒鉛結晶は、炭素が6個から成る共有結合で、その中にπ結合と呼ばれる電子が自由に飛び回りやすい二重結合を含んでいますので、金属のように熱伝導率が高い物質です。この自由電子が面方向に動き回るため、面方向の熱伝導率が極めて優れていますが、厚さ方向への熱伝導率は、平面方向に比べて1/500以下とほとんどありません。
Zebroブロックは、黒鉛単結晶のグラフェンが幾重にも重なっている厚さ30~100μm程度の黒鉛シートを接着剤で数百層に積層した黒鉛と接着剤樹脂から成る積層複合材です。
Zebroブロックをイラストの青い点線のようにスライスカットし、90°寝かせてZebroシートとし、放熱用TIMとして使用します。このように90°回転させることで、面方向の優れた伝熱特性は、垂直方向へ向きが変えられます。
黒鉛シート間の接着剤層は、可能な限り少量になるように調整され、多くの空隙や気泡、貫通孔を含んでいます。いわゆるスポンジのような構造をしています。このため、TIMとして用いた時に界面に空気溜りを残す心配がありません。また、この接着剤は、硬化後にゴムのように伸び縮みしますので、凹凸界面で黒鉛シートの密着性を向上させることができます。
【Zebroの「代表特性」】
熱伝導率:
ここに表示している熱伝導率は、理想状態のレーザー法による計測値です。実際にご使用いただく際には、面圧などにより黒鉛の内部構造が乱れることで、おおよそ半分程度の熱伝導率が実効値となります。
面方向は、 X 軸方向が Z軸方向と同じ値となり、 Y 軸方向は接着剤層があるためにほぼ0W/(m・K)になります。 よって、面方向は、(X+Y)/2となり、計測値とほぼ一致しています。
耐熱温度:
黒鉛は、酸化が無ければ3000℃以上まで耐えることができます。ここで示す温度は、柔らかな接着剤がその特性を維持しながら耐える温度です。Zebroは、リフロー工程などで、260℃/5分間程度ですと耐えることができます。
難燃性:
UL95-V0相当とは、黒鉛シートが上下方向で測定したときの結果です。複合材料のため、測定条件により結果が異なります。実装条件に合わせた認定が必要な場合には、お問合せください。
電気抵抗:
Zebroは、黒鉛を含んでいますので電気をよく通します。電気抵抗測定時に黒鉛結晶平面方向か積層方向かのどの部分に触れたかによって測定数値が大きく異なります。
シロキサンガス・オイルブリードフリー:
Zebroで使用している接着剤にシリコーン材料を含んでいません。このため、長期間のご使用でもシロキサンガスやオイルブリードが発生いたしません。
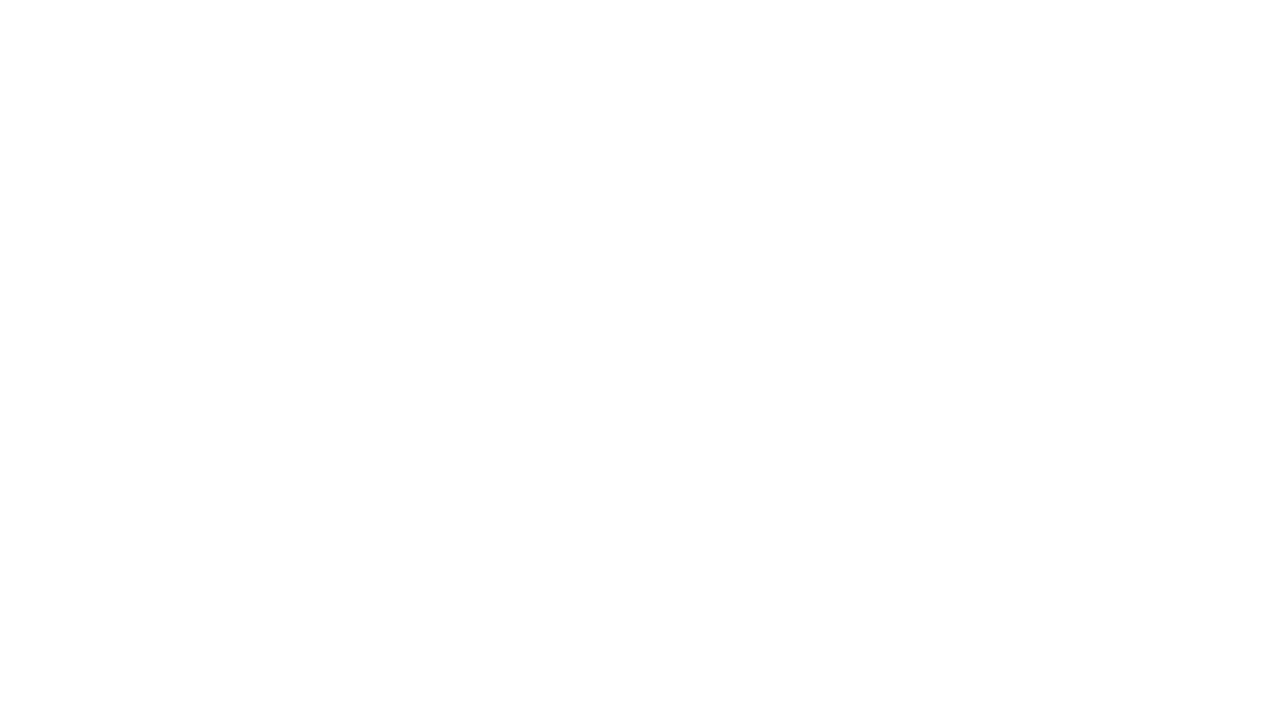
【Zebro一言メッセージ】
従来のグリスやシリコーンエラストマーとZebroの使用方法は、大きく異なります。Zebroを有効にご活用いただくためには、Zebro表面を相手面に密着させるための “面圧” と熱伝導率が極めて優れていることを活かして、 “狭い面積” で均一に面圧を掛けることが性能を十分に発揮させるためのノウハウになります。
どうしてもボルト締めなどによって面圧が掛けられない時には、Zebro表面にメッキ処理を施し、ハンダ付けで密着性を向上させることも可能です。
Zebroは、可能な限り接着剤樹脂を少量にしていますので、長期間のご使用による樹脂成分の劣化や空気溜まりによる接触熱抵抗の影響を抑えることができます。
【グリス密着時の課題】
グリスは、柔らかいために界面の凹凸に容易に入り込んで接触熱抵抗を小さくしてくれます。しかし、塗布方法に熟練が必要で、空気溜りや微細な泡を残してしまい、大きな熱抵抗となってしまう場合があります。このために加熱・冷却界面を鏡面加工程度に平滑化する必要があります。
Zebroは、面圧をお掛けいただくことで表面の黒鉛が変形して、界面の凹凸に入り込み、接触熱抵抗を極めて低く抑えてくれますので、加熱・冷却界面を平滑化する必要はありません。このためにZebro導入により加工コストを低く抑えることができます。
グリスは、熱伝導率が小さいために塗布量を少なくして、0.1mm以下などと薄くする必要があります。加熱側の界面が加熱により膨張して、うねりが生じた時に加熱面が薄いグリスを突き抜けて冷却面へ衝突し、グリス層に空気が侵入する可能性があります。
熱伝導率が高いZebroでは、グリスの0.1mmは、Zebroを厚くして1.8mmとしても同じ性能になりますので、伝熱向上に期待して0.5mm程度のZebroを用いることで、放熱量を向上させながら加熱・冷却板の衝突による熱抵抗増加を回避することができます。
【なぜ、厚さを維持しながら低熱抵抗になるのか】
右の写真は、Zebroを真上から撮影した拡大写真です。黒鉛シートと樹脂層が幾重にも積層されて、面を構成していることがわかります。また、筋状に黒く見える部分は、接着剤が少ない貫通した空隙層になります。この空隙の存在で、Zebroの表面状態が変化しやすくなり、密着性の向上などに役立ちます。
上から下へと水色の線で表面の凹凸状態を観察しました。この結果を左のグラフで示しています。水色の線が凸部と凹部を繰り返しており、凸部は黒鉛シートが表面に露出している部分になります。太い水色の仮想線は、界面を想定しています。凸部の黒鉛シートと仮想線は、数点が接触しているのみで、Zebroと相手側の面とでは、ほとんど密着していないことがわかります。
このようにZebroが無加圧の時には、接触熱抵抗が非常に大きいと言えます。密着性を良くするためにZebroへ押圧を掛けることで、接触抵抗が著しく低下します。
【Zebro表面の凹凸状態 その2】
上のカラー写真は、Zebro表面の凹凸状態を色別に示しています。赤色は凸部で、緑色は凹部です。前頁のグラフに比べて、広い範囲(約30mm)を観察しています。下のグラフから黒鉛シートの高低差が約20μm程度であることがわかります。
黒鉛シートと樹脂層との積層面は、 前頁のそれぞれの層の凹凸を含みながら、大きなうねりも存在しており、これらの凹凸やうねりが押圧することで変形し、相手面と密着します。
【密着性の向上 押圧による黒鉛シートの圧縮】
右上のグラフは、Zebro高熱伝導品を上面方向から加圧した時の圧縮量を示しています。同様に、 右下のグラフは、標準品の加圧-圧縮量を示しています。
Zebro上面から押圧していくと、0.05MPa-0.02~0.03mm付近まで急激に圧縮され、それ以上の押圧では、緩やかに圧縮されています。つまり、Zebroは、2段階で圧縮されるという特徴を持っています。
この1段階目での圧縮は、前頁で示した黒鉛シート表面の凸部が小さな押圧でつぶれた、凹凸段差に相当する収縮である事がわかりました。 この時のZebroと相手面との界面の状態を次頁のイメージ図で示しました。
2段階目の収縮は、次々頁の写真で示すように垂直に配置された黒鉛シートが上方からの押圧で弓なりに曲がることで収縮していることが分かりました。
以上の様に少なくとも押圧1.2MPaまでは、Zebroの収縮変形が滑らかで、Zebro構造が破壊されることなく維持されていることが伺えます。実績では、10MPaでご使用いただいているお客様もいらっしゃいます。
【①の圧縮 黒鉛シート突起部の潰れ】
Zebroと加熱・冷却面との界面の状態を拡大イメージ図で表現しています。加熱・冷却面がザラザラした凹凸面であっても、Zebroの薄い黒鉛シート(グラフェン)がつぶれることで繊細に凹凸内部に食い込み、黒鉛シートと加熱・冷却面との密着性が著しく向上します。
また、各黒鉛シートは、多くの気孔を含むゴムの様に柔らかな樹脂で接着されていますので、黒鉛シートがバラバラに飛び散る事がありません。さらにこのスポンジ状の接着剤樹脂により、黒鉛シートを緩やかに上下させて、界面の大きなうねりに対しても追従して密着してくれます。
【②の圧縮 高熱伝導品:黒鉛シートの弓なり変形】
押圧0.05MPa以上では、黒鉛シートが右上写真のように弓なりに変形して、Zebroシートの厚さ方向が圧縮します。元々、黒鉛結晶は平坦ですので、弓なりに変形した黒鉛シートは、常に真っすぐになろうとして、Zebro内部には厚さ方向へ伸びようとする応力を残存しています。また、接着剤樹脂もゴムが引張られた状態で実装されていますので、厚さ方向へ伸びようとする応力が残存しています。ただし、接着剤樹脂の残存応力は、長期間のご使用で徐々に弱くなりますが、黒鉛結晶の残存応力は維持されると予想しています。
【Zebroシートの熱抵抗】
右下のイメージ図は、ZebroをTIM(放熱シート)としてご使用いただく際の熱抵抗モデルです。接触式熱抵抗測定装置で計測される全熱抵抗値は、Y=aX+bで表されます。
ZebroのTIMシートを毎日16サンプル以上測定し続けていますが、全ての測定点は、この式に当てはまります。つまり、Zebroの界面における熱抵抗値が全てのサンプルで安定している事を示しています。
Zebroは、熱伝導率が高いためにaXが小さな値になり、Zebro面に押圧を掛けることで密着性が良くなり、接触熱抵抗のb値が小さくなります。
【Zebroシートの「厚さ-熱抵抗の関係」】
グラフ中の水色の線は、熱伝導率が30W/(m・K)の銀ペーストの厚さと熱抵抗値の関係を示しています。緑色の線は、Zebroに0.5MPaの面圧を掛けた時の厚さと熱抵抗値の関係を示しています。Y軸切片であるb値は、放熱材が無い時の接触熱抵抗に相当し約0.04℃・㎠/Wを示しています。
現状のCPUやGPUでTIM(放熱シート)を使用する際には、0.5MPa程度で押圧してお使いいただくケースが多いようです。また、多くのお客様では、縦軸の熱抵抗値が0.2℃・㎠/W以下になるように放熱材の肉厚を調整しています。例えば、第6世代の通信規格では、熱抵抗値として0.13~0.15℃・㎠/W程度が必要になりそうです。
例えば、既存品例[30W/(m・K)]の熱抵抗値を0.1℃・㎠/Wにしたい時、厚さは、約0.25mm以下である必要がありますが、Zebroでは、厚さが約1.8mmでも同じ熱抵抗値になります。また、Zebroが0.25mmの時には、約0.045℃・㎠/Wと著しく低い熱抵抗値になります。
※Zebroの0.25mmは、無加圧時の厚さ0.3mmで押圧0.5MPaを掛けた時の実際の厚さに相当します。
【Zebroシートの「厚さ-熱抵抗」】
右上のグラフは、Zebro高熱伝導品の厚さと熱抵抗の関係を示しています。また、右下のグラフは、同様に標準品の測定結果を示しています。各色の直線は、0.276MPa(40psi),0.5MPa,1.0MPaで押圧しながら熱抵抗値を測定した結果です。
Zebroへの押圧を高くすると、傾きはあまり変化せずに※1. Y軸切片のb値が小さくなり、押圧1MPaでは、100%接触に近い熱抵抗値が約0℃・㎠/Wになります。つまり、グリスと同等以上の密着性になります。
※1. 直線の傾きがわずかに変わる理由として、黒鉛シート内部の構造変化に起因していると考えられます。